What happens when a customer returns your product due to a manufacturing flaw? The cost isn’t just a refund. It’s your brand reputation, potential repeat sales, and even relationships on the line.
For importers sourcing high-end consumer goods from China, product inspection is not a nice-to-have, it’s a quality assurance imperative.
With major production zones in Shanghai and Guangdong, and satellite hubs across Vietnam and Hong Kong, manufacturers operate at high volumes and varying levels of oversight. Without rigorous on-site inspections, quality issues can slip through, leading to costly rework, lost shipments, or worse, consumer safety concerns.
The Role of Product Inspection in Supply Chain Resilience
At its core, product inspection is about mitigating risk. Quality inconsistencies can derail an otherwise solid supply chain. Inspection services integrate seamlessly into your production process to help identify and resolve potential defects, ensuring the product meets the agreed-upon quality requirements and standards.
High-end brands don’t just rely on post-production fixes. They bake quality control into each phase: from raw materials to final packaging. With a product inspection service like Silq, you can protect your brand reputation and elevate customer satisfaction.
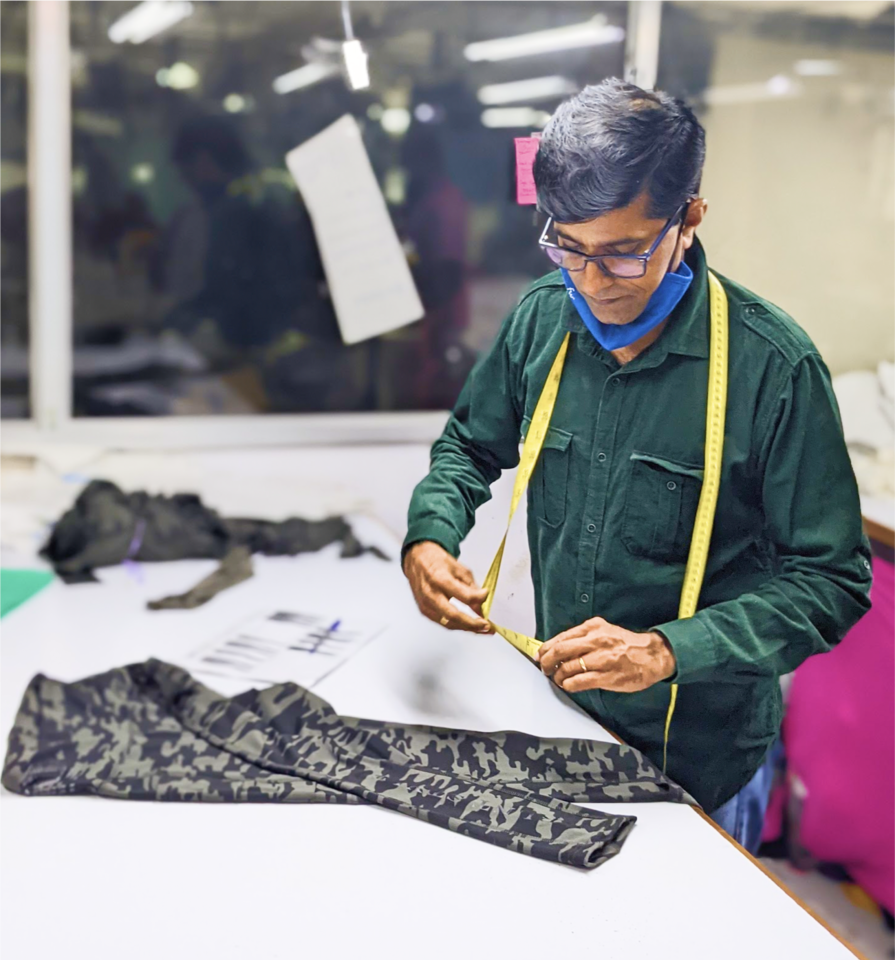
When to Use Product Inspection?
Product inspection services don’t need to blanket every process; they need to target failure points where quality issues become financial risks. Here’s where inspections deliver the highest ROI:
Final Stage Risk: Before Shipment
- Most returns stem from packaging errors, incorrect labeling, or cosmetic defects that were missed during final checks.
- A pre-shipment inspection using proper AQL sampling helps ensure the batch meets your quality standards and avoids penalties.
Read More: Pre-Shipment Inspection Guide [Free Checklist Inside]
High-Defect Product Categories
- Sectors such as textiles and consumer goods often experience frequent defects due to complex components or inconsistencies in finishes.
- On-site inspections with precise quality control requirements can catch non-compliance before products reach your warehouse.
Supplier Transitions or Scaling
- Scaling production with new or less-established Chinese suppliers increases risk.
- Conducting a compliance audit or third-party random inspection early in the production process helps protect quality assurance from the outset.
When Returns or Complaints Spike
- A sudden uptick in return rates or warranty claims? Quality inspection services can help pinpoint whether the issue is with raw materials, poor assembly, or a deviation from specifications.
- Detailed reports from a reliable service provider enable sourcing teams to identify and address issues at their root cause, thereby reducing rework.
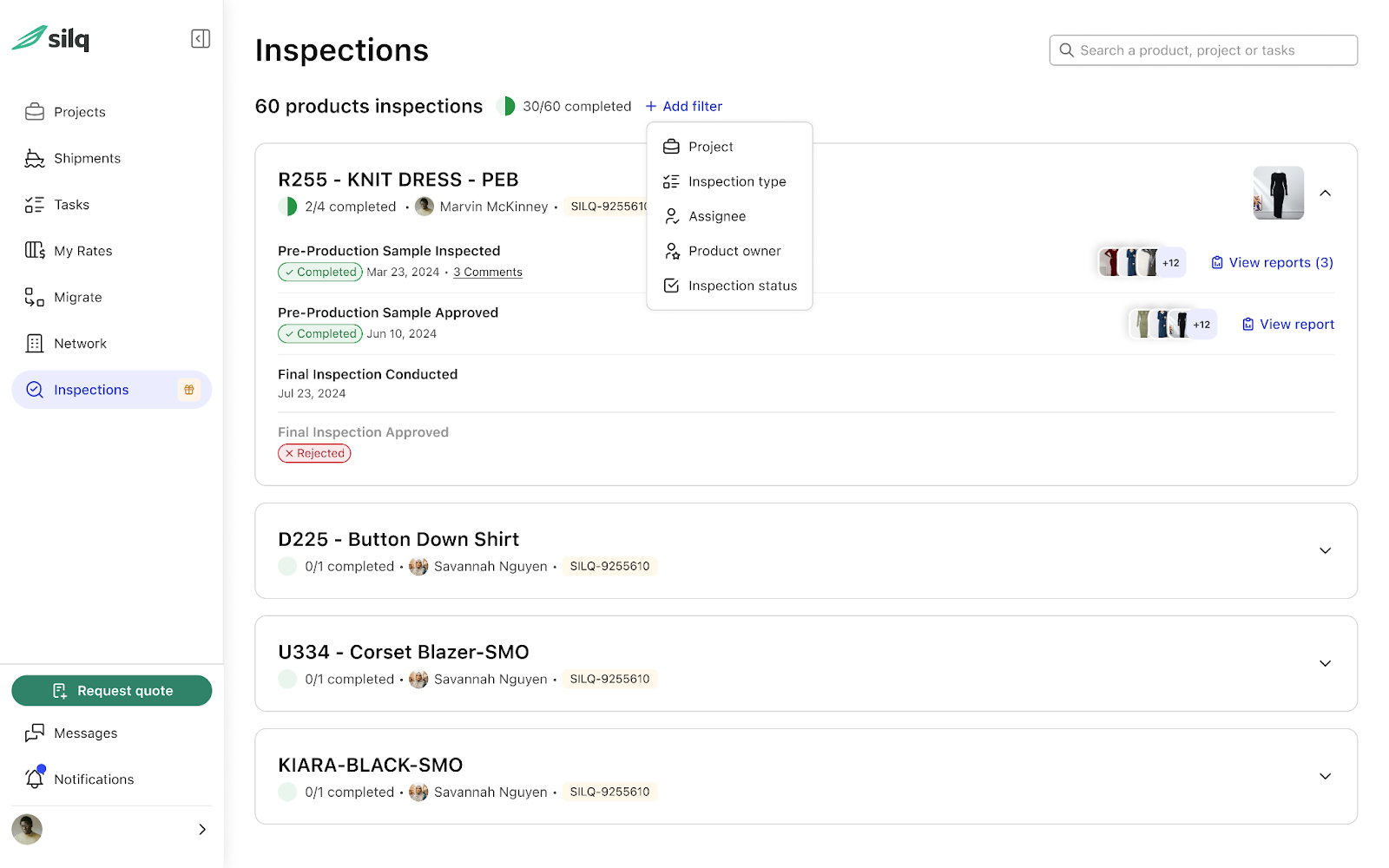
Why Third-Party Inspection Companies Outperform In-House QC
While some brands rely on in-house teams, many lean on an experienced third-party inspection company to cover ground across diverse regions. Third-party providers like Silq provide:
- Unbiased audit services
- Local, on-site experts
- Compliance with ISO standards and regulatory requirements
The result? Objective, detailed reports that help you make fast, data-backed decisions.
What a Good Inspection Report Should Include
A professional inspection report should be more than a checklist. Look for:
- High-res photos of defects and packaging
- Description of sampling methodology and AQL results
- Notes on functionality, measurements, and appearance
- Compliance audit findings, if relevant
- Inspector commentary with recommendations
These reports give product development and sourcing teams immediate insight into whether a batch meets quality control standards.
Download a Silq Sample Report.
Cost Considerations: What Does a Man-Day Include?
Pricing for inspection services in China typically ranges from $200 to $300 USD per man-day, depending on location, urgency, and product type. While some may hesitate at the upfront spend, here’s the reality:
- A failed inspection could avoid a costly defective shipment
- One container loading supervision can prevent thousands in returns
- A proper factory audit filters out unreliable partners early on
When you view inspections through the lens of cost avoidance, it becomes a small price for supply chain insurance. Silq offers product inspections starting at $99/product, helping you accelerate product development by leveraging on-site evaluations prior to shipping. Talk to an expert to get started.
Common Quality Issues Identified in China Inspections
Inspections routinely uncover:
- Incorrect product dimensions or colors
- Missing or incorrect labeling
- Defects in textiles, stitching, and adhesives
- Inadequate packaging for long-haul freight
- Substituted raw materials
By catching these pre-shipment, brands avoid damage to their reputation and customer satisfaction.
Read More: 5 Factory Inspection Mistakes & Best Practices for Quality Control
Inspection as a Strategic Supply Chain Tool
A well-integrated quality inspection program doesn’t just fix flaws – it improves your sourcing intelligence. Inspection data can:
- Feed supplier scorecards
- Highlight weak points in the manufacturing process
- Inform decisions about future orders or rework potential
And when shared cross-functionally (between sourcing, logistics, and product), it supports continuous improvement and tighter quality assurance.
Build Inspection Into Your Sourcing Playbook
Whether you’re working with established factories in Shanghai or exploring new partners in Vietnam, inspections remain a non-negotiable step in any high-quality sourcing model. Use trusted service providers with transparent pricing, meaningful inspection reports, and broad regional coverage.
Investing in product inspection isn’t just about catching defects — it’s about building a supply chain that performs, protects, and profits.
Need help reducing returns and improving product quality?
Silq offers end-to-end quality control services, including factory audits, quality control inspection services in China, Vietnam, India, Bangladesh, Pakistan, and Indonesia. Let’s make quality your competitive edge.
Frequently asked questions
Yes, even ISO-certified factories can have lapses; inspections catch issues before they reach your customers.
Ideally, when 100% of goods are produced and at least 80% are packed, to ensure accurate quality control.
Yes, qualified inspection teams can oversee container loading at major ports across China, Hong Kong, and Vietnam.
Product inspection is an on-site visual and functional check; product testing is done in a lab to verify compliance or safety.
At least once a year, or more frequently if past inspections revealed defects or non-compliance.